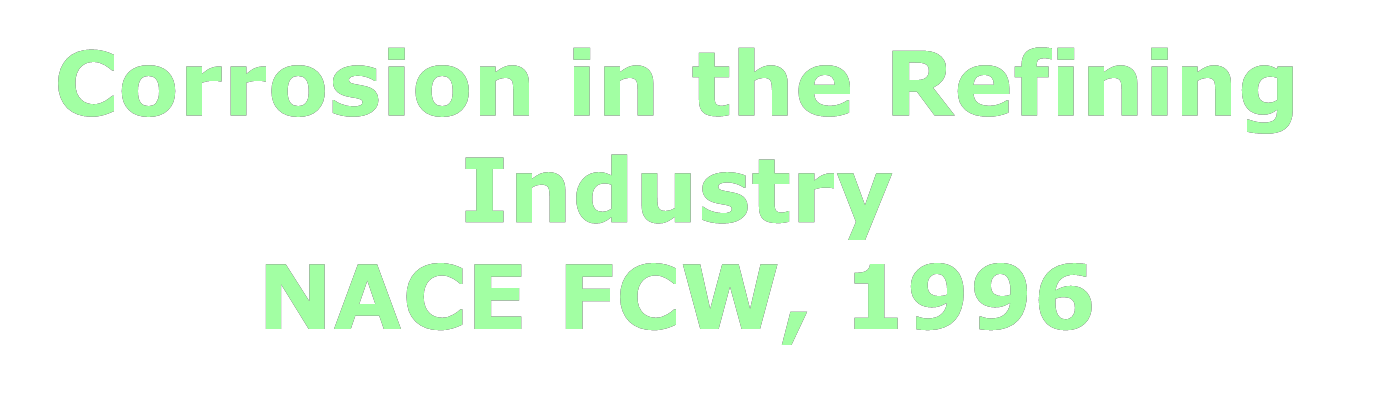
Corrosion in the Refining
Industry
NACE FCW, 1996
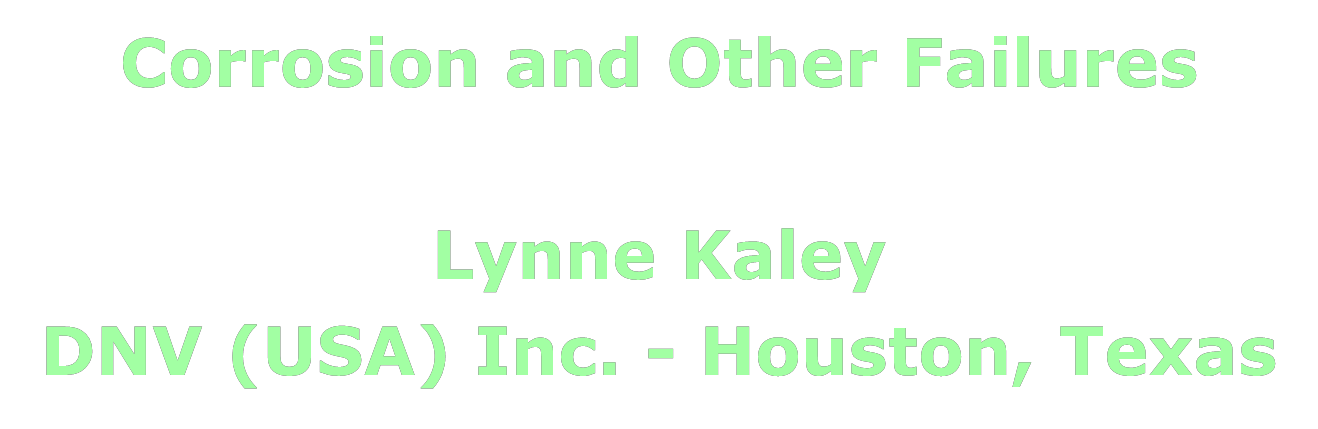
Corrosion and Other Failures
Lynne Kaley
DNV (USA) Inc. - Houston, Texas
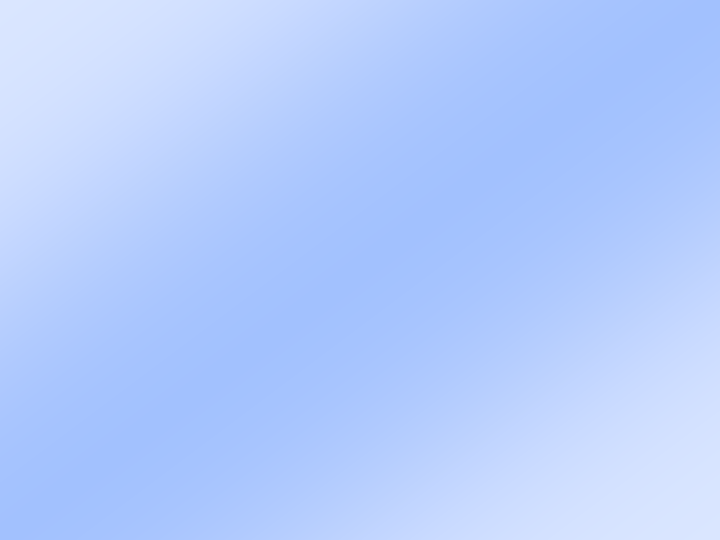
NACE Corrosion in the Oil Refining Industry
•
•
•
Purpose
Brief overview of the types of corrosion and
other deterioration mechanisms active in
typical refinery processes
Discussion of corrosion and other types of
damage occuring at high and low temperature
conditions
Description of low and high temperature
corrosion principles and the process conditions
that drive them
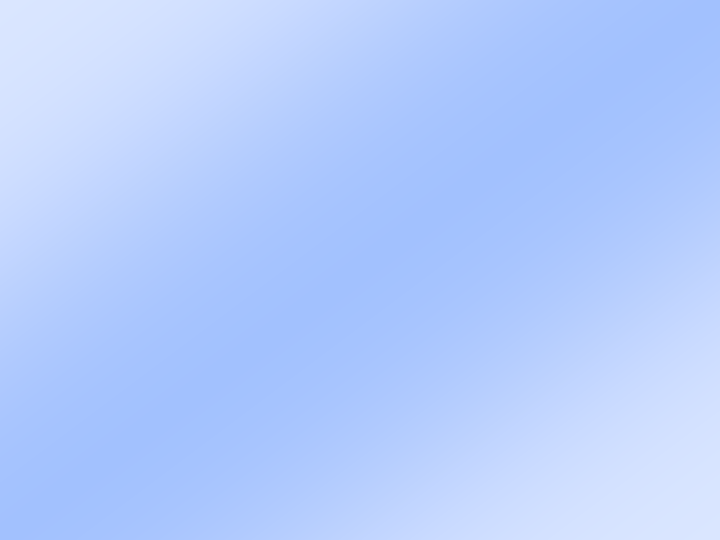
NACE Corrosion in the Oil Refining Industry
•
•
•
•
•
•
Low Temperature Corrosion
Below 500OF (260OC)
Presence of water (even in very small
amounts)
Electrolyte in hydrocarbon stream
Obeys electrochemical laws
Stable films can reduce or prevent corrosion
Vapor streams - at water condensation points
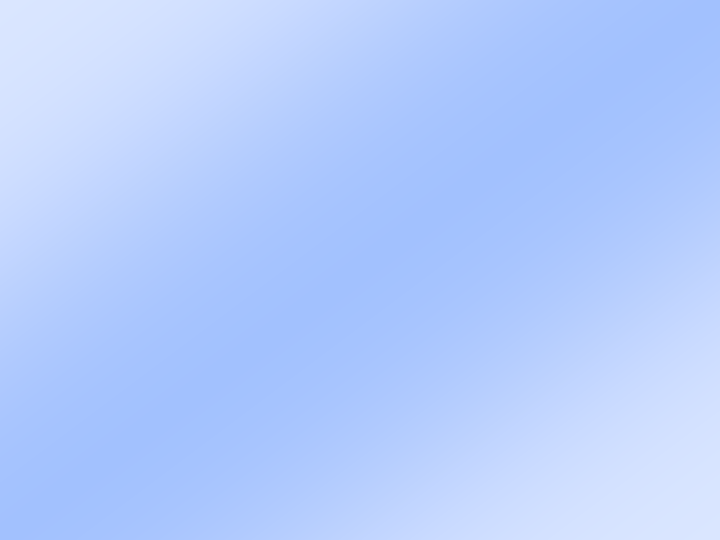
NACE Corrosion in the Oil Refining Industry
•
•
•
High Temperature Corrosion
Above 500OF (260OC)
No water present
Result of a reaction between metal and
process ions (such as oxygen, sulfur,
etc.)
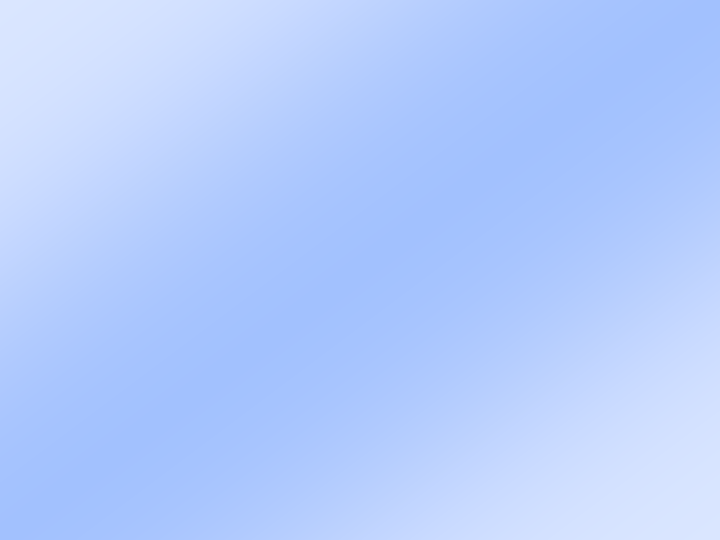
NACE Corrosion in the Oil Refining Industry
•
•
•
•
•
Causes of Deterioration
Normal operation, upset, startup/shutdown
conditions
Refineries contain over (15) different process
units
Material/Environment condition interactions
Many combinations of corrosive process
streams and temperature/pressure conditions
In the absence of corrosion, mechanical and
metallurgical deterioration can occur
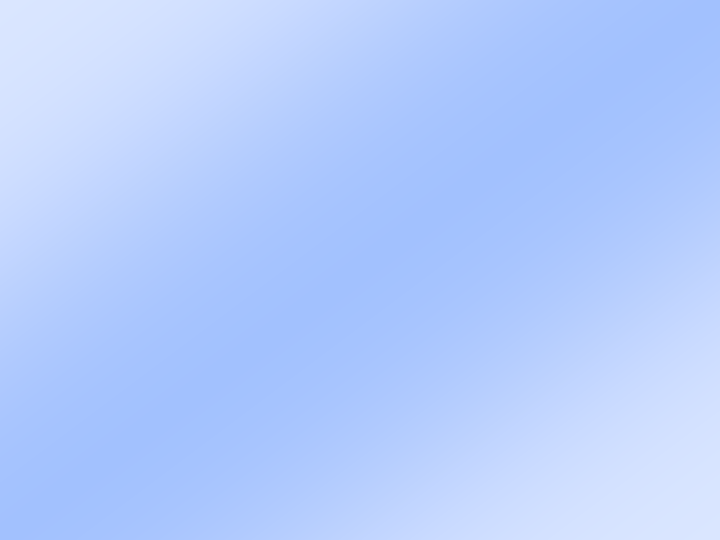
NACE Corrosion in the Oil Refining Industry
Types of Damage
• General loss due to general or localized
corrosion
• Stress Corrosion Cracking
• High Temperature Hydrogen Attack (HTHA)
• Metallurgical Changes
• Mechanical Failures
• Other Failures
Damage types occur with specific combinations of
materials and environmental/operating conditions
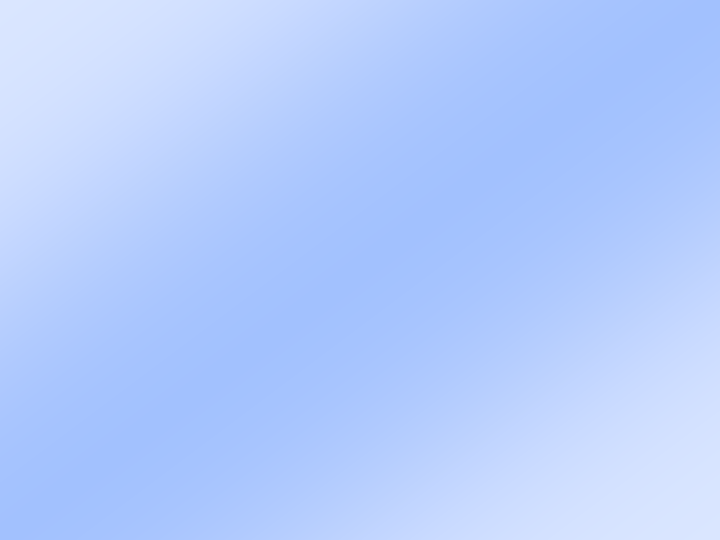
NACE Corrosion in the Oil Refining Industry
•
•
Corrosion Principles
Corrosion rate is measured as weight loss
per unit area and is expressed in mils per
year (mpy)
Rates can be affected by:
– Passivity forming protective surface films
(including corrosion inhibitors, paints and
coatings)
– Oxygen content
– Flow velocity/rates
– Temperature
– Acidic conditions
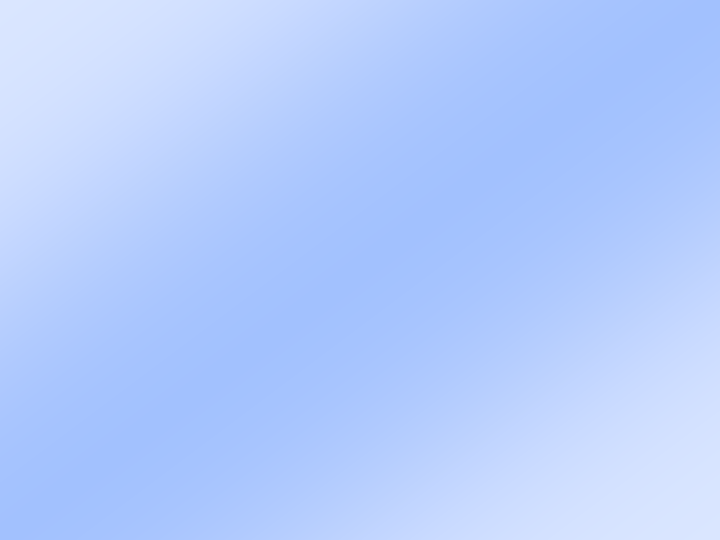
NACE Corrosion in the Oil Refining Industry
•
•
•
•
Process Corrosion
Low Temperature Conditions
Not caused by hydrocarbons
Caused by inorganic compounds such as
water, hydrogen sulfide, hydrogen chloride,
sulfuric acid, etc.
Crude oil contaminants
Process chemicals
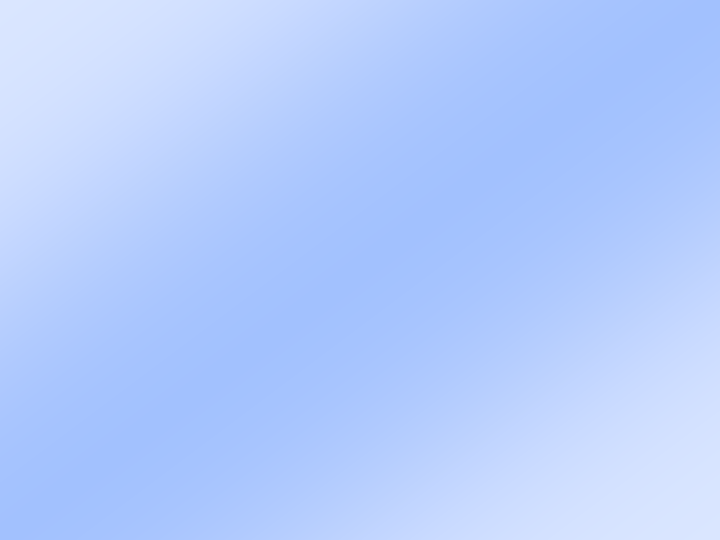
NACE Corrosion in the Oil Refining Industry
•
•
•
•
Process Corrosion
High Temperature Conditions
Important due to serious consequences
High temperatures usually involve high
pressures
Dependent on the nature of the scale formed
– general thinning
– localized thinning (pitting)
– intergranular attack
– mixed phase flow
Corrosion due to sulfur compounds most
common and well documented
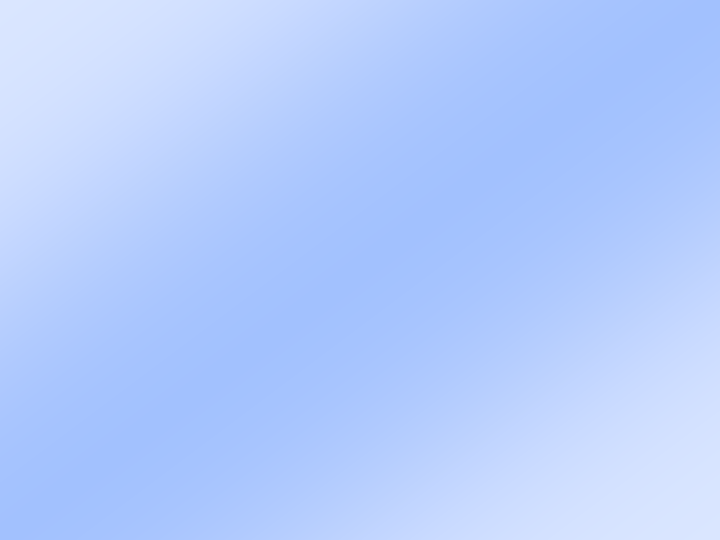
NACE Corrosion in the Oil Refining Industry
Corrosives Found in Refining
Sulfur
Naphthenic Acid
Polythionic Acid
Chlorides
Processes
Present in raw crude. It causes high-temperature
sulfidation of metals, and it combines with other
elements to form aggressive compounds, such as
various sulfides and sulfates, sulfurous, polythionic,
and sulfuric acids.
A collective name for organic acids found primarily
in crude oils from western United States, certain
Texas and Gulf Coast and a few Mid-East oils.
Sulfurous acids formed by the interaction of sulfides,
moisture, and oxygen, an occurring when equipment
is shutdown.
Present in the form of salts (such as magnesium
chloride and calcium chloride) originating from
crude oil, catalysts, and cooling water.
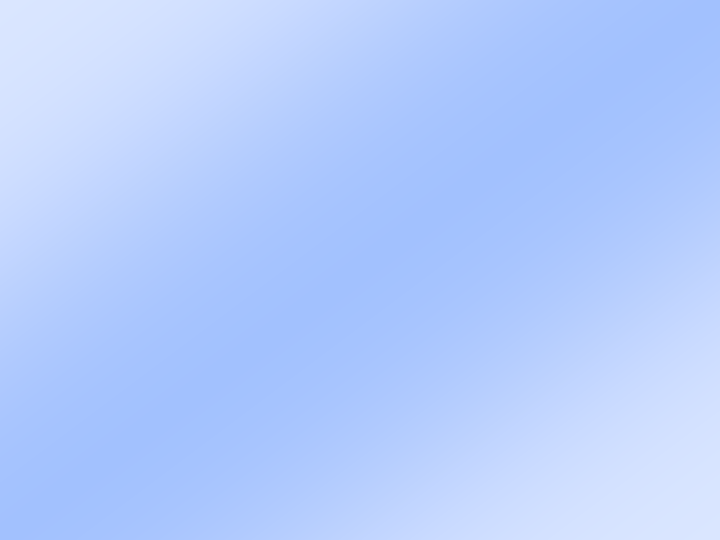
NACE Corrosion in the Oil Refining Industry
Corrosives Found in Refining
Carbon Dioxide
Ammonia
Cyanides
Processes
Occurs in steam reforming of hydrocarbon in
hydrogen plants, and to some extent in catalytic
cracking. CO2 combines with moisture to form
carbonic acid.
Nitrogen in feedstocks combines with hydrogen to
form ammonia - or ammonia is used for
neutralization - which in turn may combine with
other elements to form corrosive compounds, such as
ammonium chloride.
Usually generated in the cracking of high-nitrogen
feedstocks. When present, corrosion rates are likely
to increase.
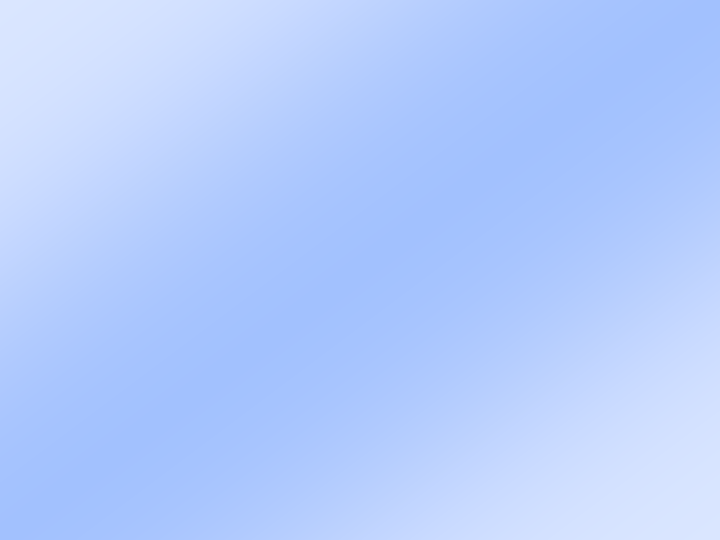
NACE Corrosion in the Oil Refining Industry
Corrosives Found in Refining
Hydrogen Chloride
Sulfuric Acid
Hydrogen
Processes
Formed through hydrolysis of magnesium chloride
and calcium chloride, it is found in many overhead
(vapor) streams. On condensation, it forms highly
aggressive hydrochloric acid.
Used as a catalyst in alkylation plants and is formed
in some process steams containing sulfur trioxide,
water and oxygen.
In itself not corrosive but can lead to blistering and
embrittlement of steel. Also, it readily combines
with other
elements
to
produce
corrosive
compounds.
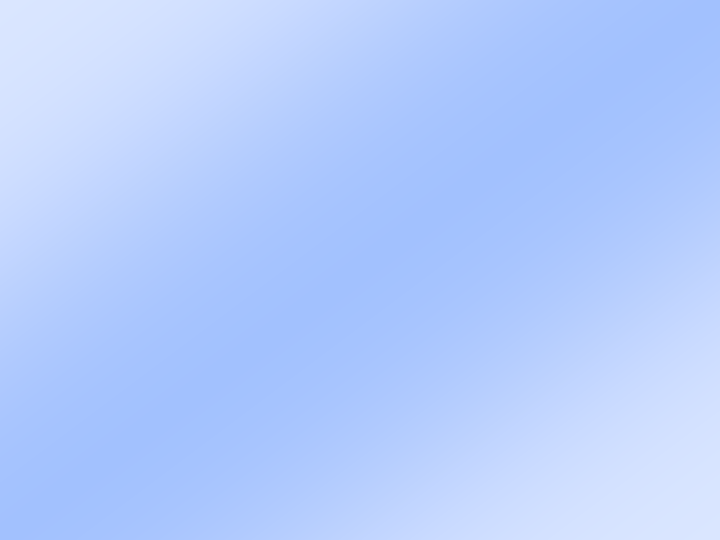
NACE Corrosion in the Oil Refining Industry
Corrosives Found in Refining
Phenols
Oxygen
Carbon
Processes
Found primarily in sour water strippers.
Originates in crude, aerated water, or packing gland
leaks. Oxygen in the air used with fuel in furnace
combustion and FCC regeneration results in high-
temperature environments which cause oxidation and
scaling of metal surfaces of under-alloyed materials.
Not corrosive but at high temperature results in
carburization that causes embrittlement or reduced
corrosion resistance in some alloys.
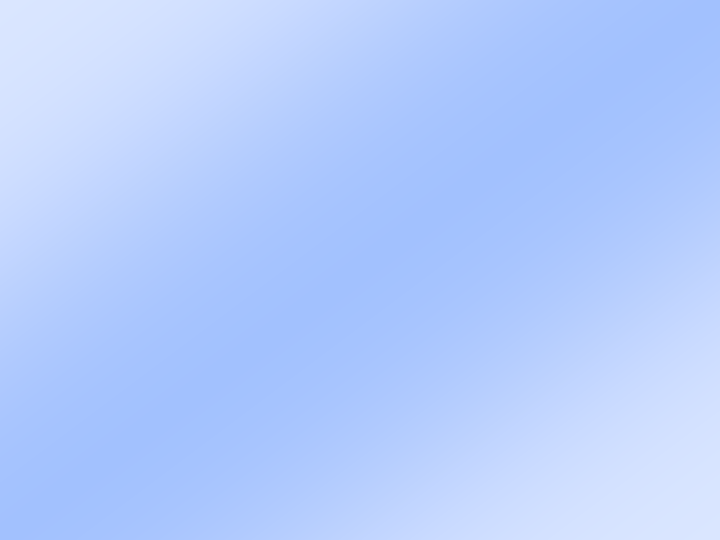
NACE Corrosion in the Oil Refining Industry
•
•
•
•
•
•
•
•
•
•
•
Metal Loss
General and/or Localized
Galvanic corrosion
• Sulfuric acid
Pitting
• Hydrofluoric acid
Crevice corrosion
• Phosphoric acid
Intergranular attack
• Phenol (carbolic acid)
Erosion corrosion
• Amine
Hydrogen chloride
• Atmospheric corrosion
Ammonia bisulfide
• Corrosion under
Carbon dioxide
insulation
Process chemicals
• Oxidation
Organic chlorides
• High temperature
Aluminum chloride
sulfidation
• Naphthenic acid
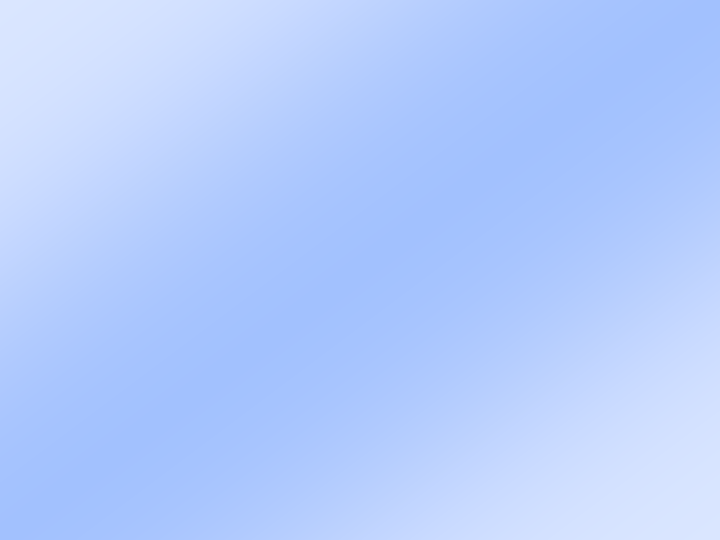
NACE Corrosion in the Oil Refining Industry