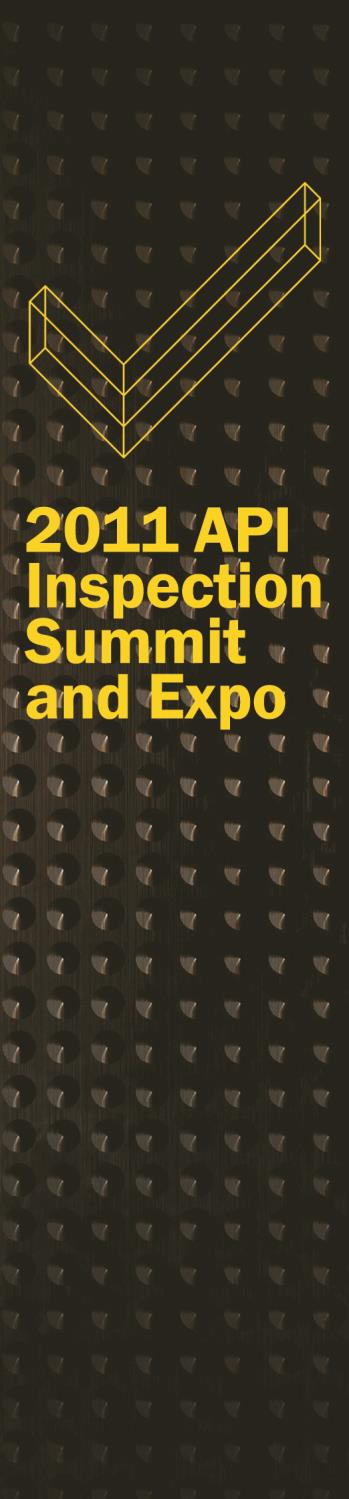
Developing Effective Inspection Plans
for Fixed Equipment Programs
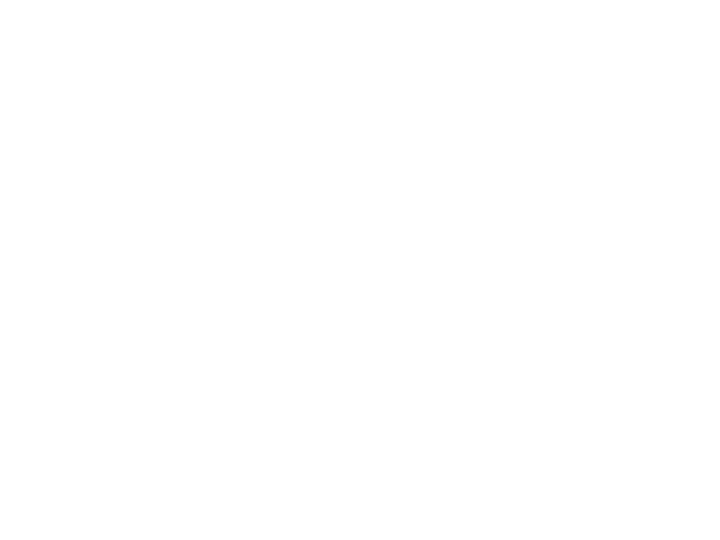
by Lynne Kaley & John Conway
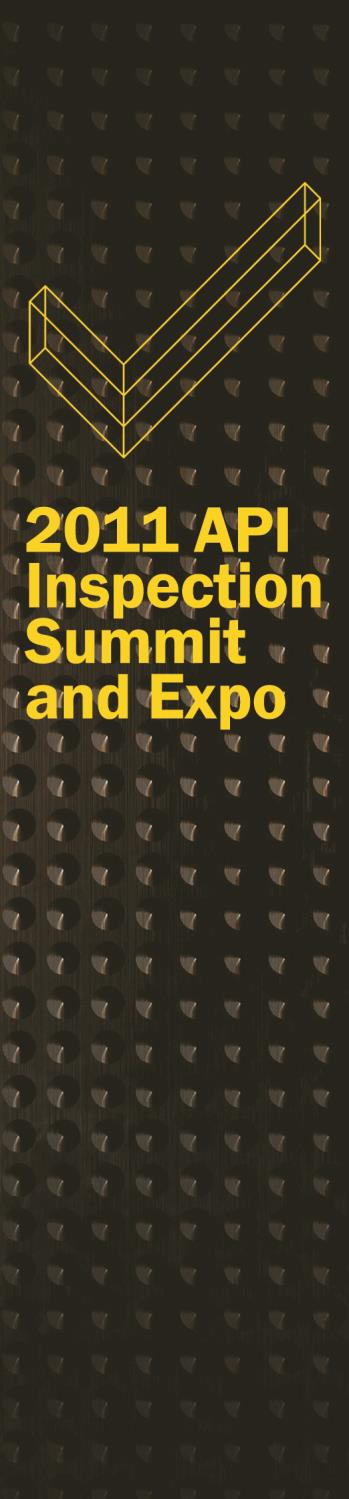
Lynne Kaley, PE
Materials/Corrosion and Risk Management Engineer
30+ Years Refining, Petrochemical and Midstream Gas
Processing Experience
10 years owner/user plant metallurgist/corrosion and
corporate engineer
20+ years consulting with plant management,
engineering and inspection departments:
• Risk-Based technology (RBI) development leader
• Development of implementation work process for plant
application
• Member of API committees for development of API 580 and API
581 recommended practices
Project Manager of API RBI Project from 1996-2009
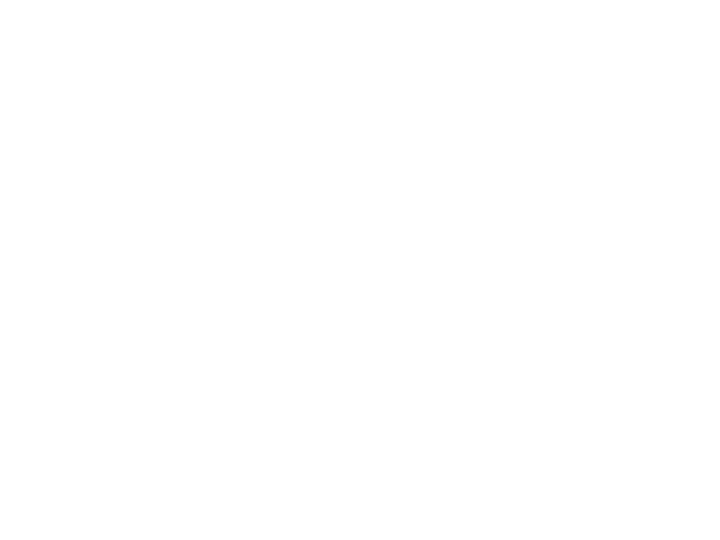
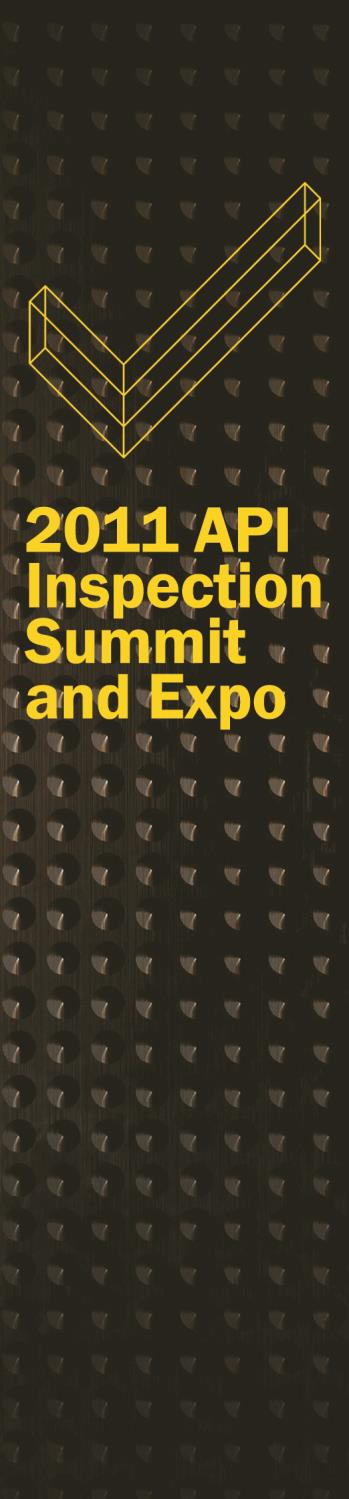
John Conway
33 years Inspection/Reliability Experience
• Owner/User
• Inspection/Reliability Management
• Inspection and RBI Consulting
Certifications/Training/Education
• National Board
• API 510 with 571 endorsement API 570, API 653
• NACE-Senior Corrosion Technologist
• BS- University of Texas at Austin
Affiliations
• API Codes and Standards Participant
• Development of recommended practices for Corrosion Under
Insulation (CUI) and Integrity Operating Windows (IOW)
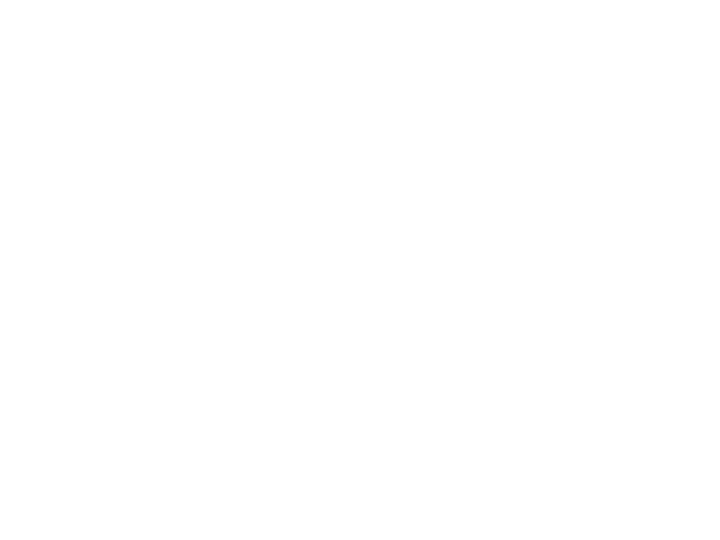
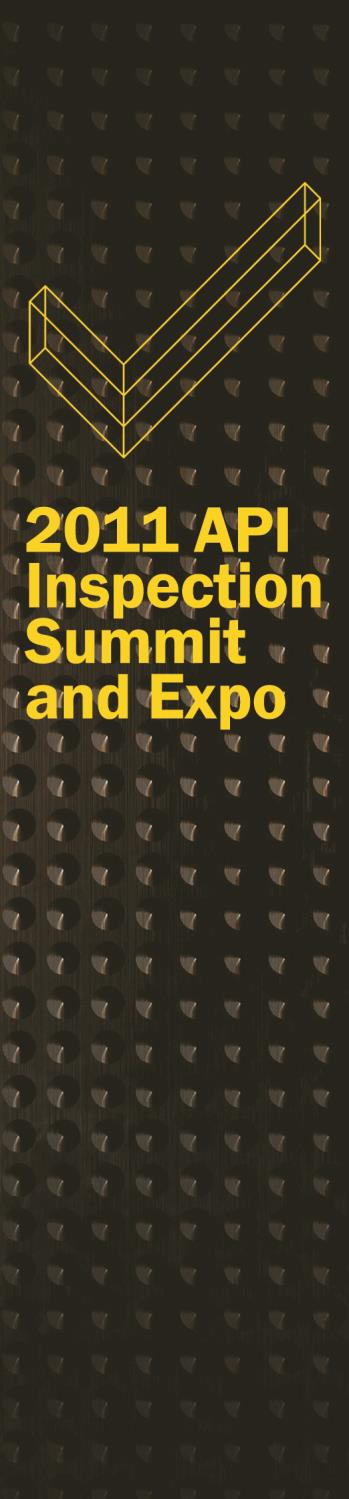
Purpose
Purpose of Presentation
• Development of effective inspection programs with or without
RBI
• Proper documentation of inspection to achieve full credit for
inspection performed
• Development of acceptance/rejection criteria prior to
conducting inspection
• Show examples to demonstrate potential challenges and how
to handle exceptions during inspection
Sources/References
• API 510, 570, 653
• API 580, 581
• API 571
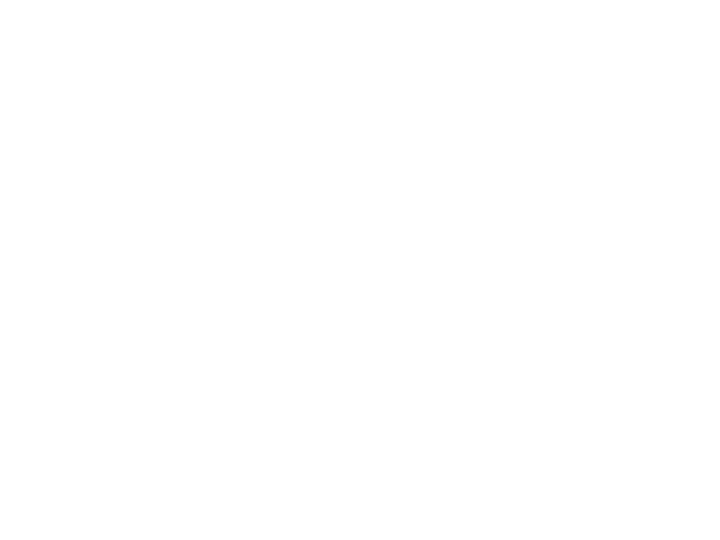
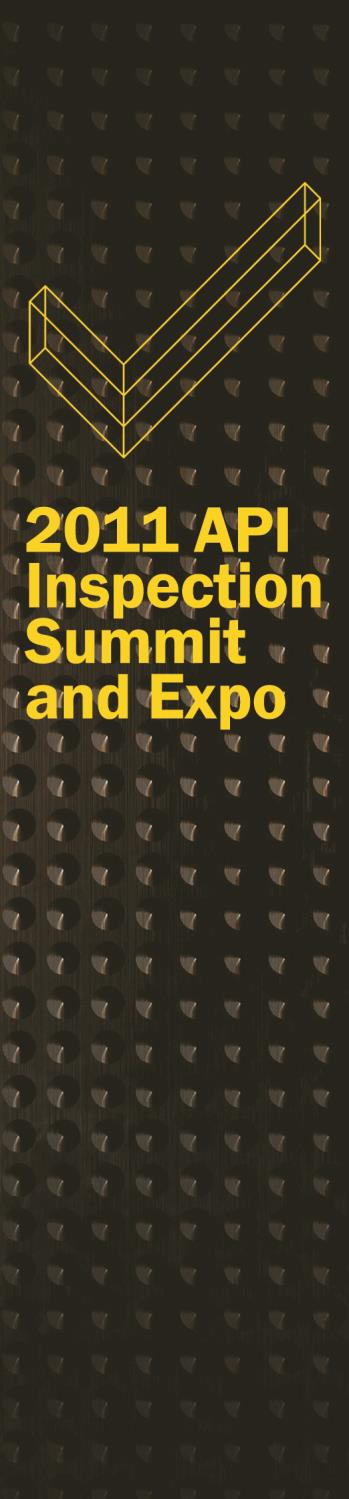
Outline
Introduction
Inspection Program Goals
Inspection Planning Process
Fixed Interval vs. Risk-Based
Cost Benefit for Risk-Based
Today’s Inspection Responsibilities
Future Inspection Programs
Industry Examples (4)
Conclusions
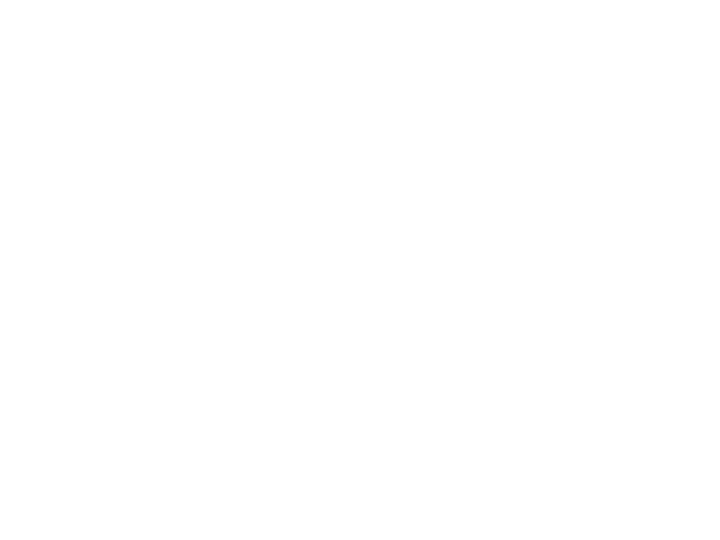
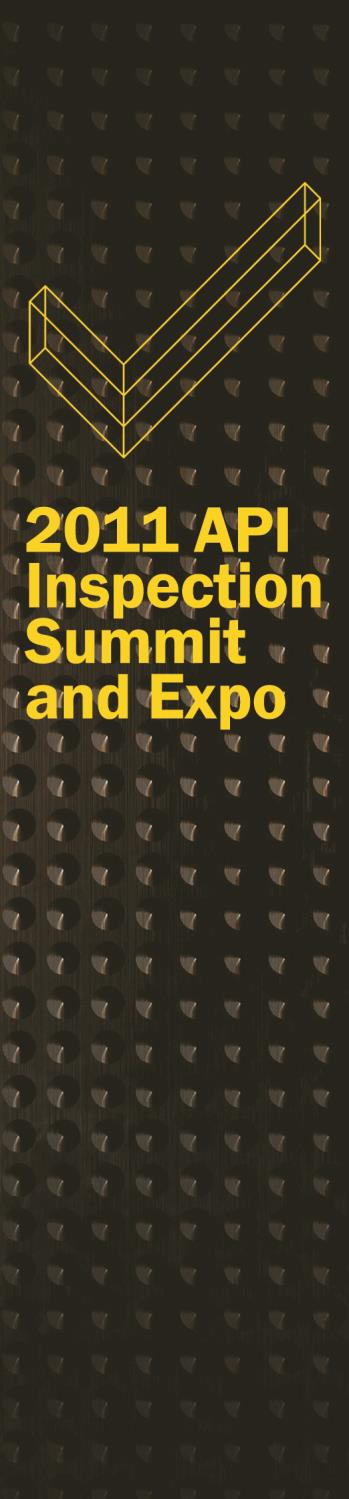
Introduction
Flood of technology and regulatory requirements since
1990 has changed inspection program management
work flow
Outsourcing inspection and engineering services has
provided additional resources and expertise but has
created a fractured work flow and introduced multiple
hand-offs
• Can introduce errors at each hand-off point
• May not achieve the same level of ownership by each party
• May not take advantage of synergy potential between parties
Inspection data analysis required to:
• Develop, evaluate and interpret inspection findings
• Provide recommendation for next inspection required
Multiple software products add complexity as well as
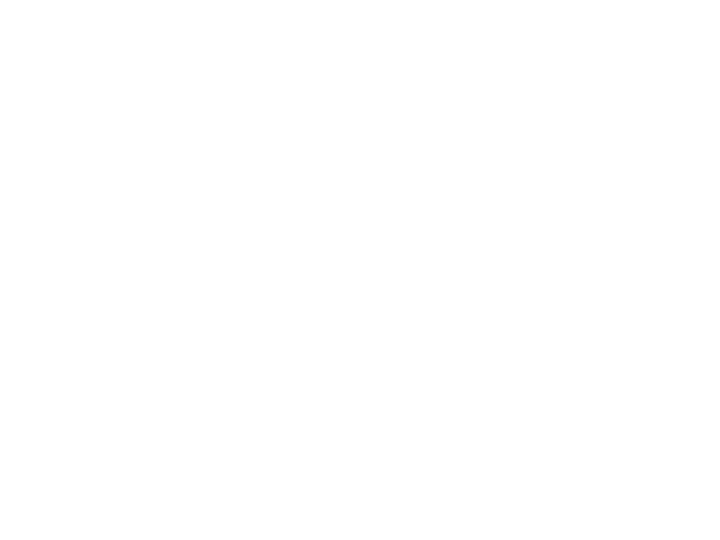
time consuming manual methods for combining results
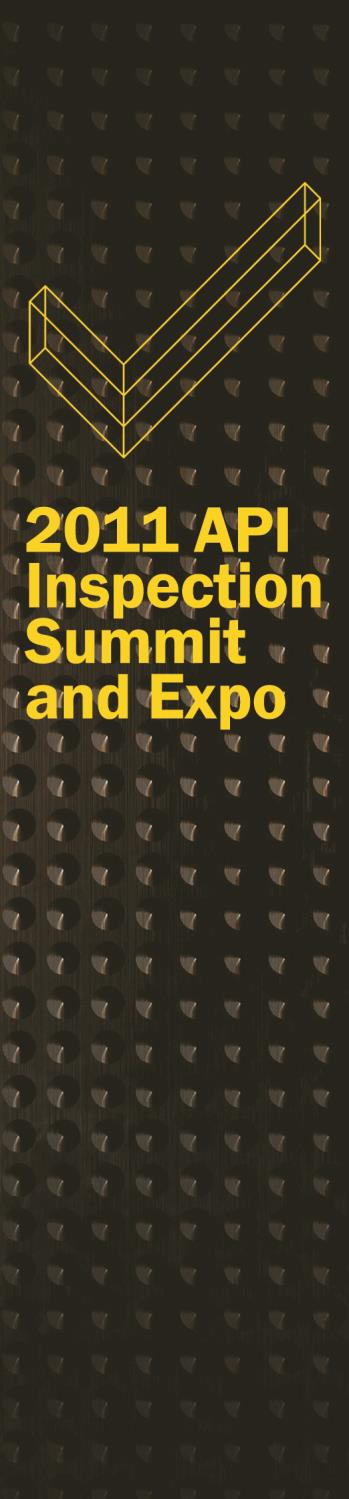
Inspection Program Goals
Assure regulatory and corporate compliance
Identify program improvements by streamlining the
workflow and eliminating, to the extent possible, time-
consuming manual activities or duplicate efforts
• Provide improved inspection data quality by being more
involved and aware of the working process
• Provide suggestions for improvements as well as better analysis
and information from the field
• Help define/design the streamlined workflow including
procedure, decision-making points, analysis and reporting
Provide added-value services for budgeted inspection
program
Develop multi-year inspection plan for scheduling and
budgeting
Provide data management and analysis, scorecard
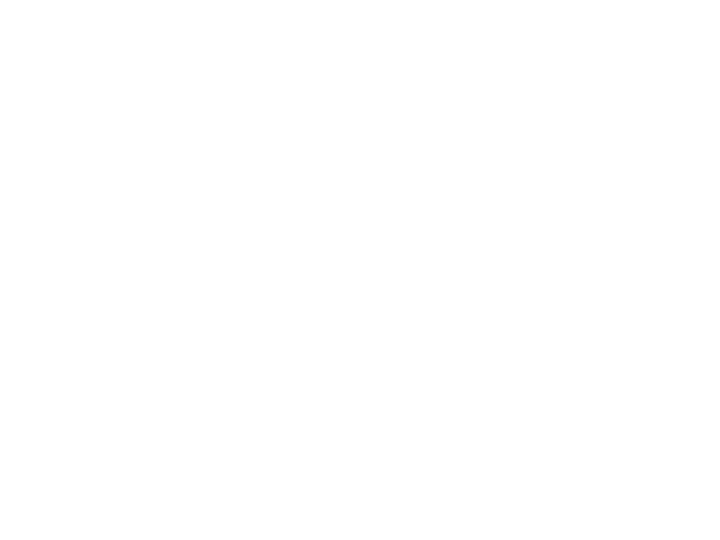
metrics and dashboard reporting
Inspection Plan Development
Reliability & Risk Compliance
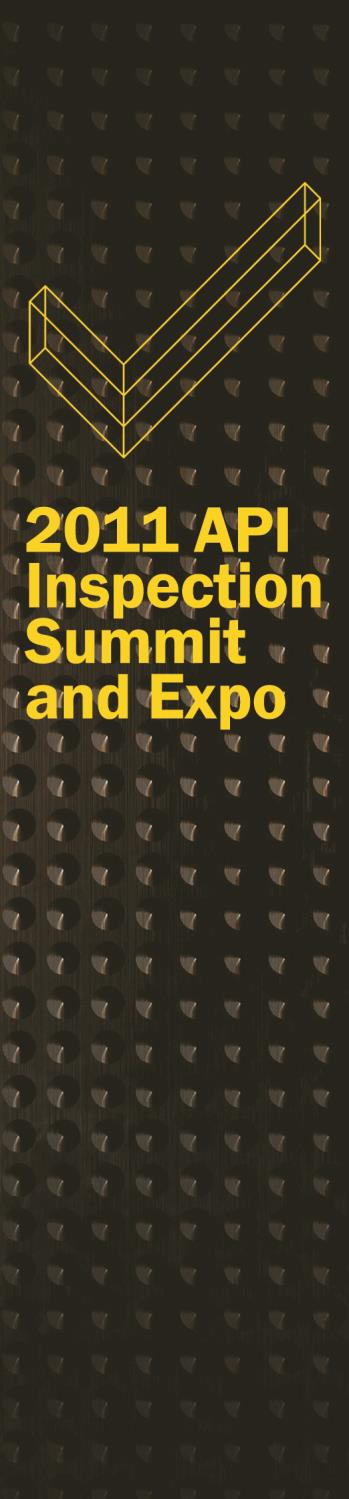

Interval Based Program
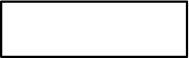

Safety & Environmental
Compliance
Baseline Inspection
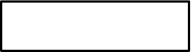
TML/CML Inspection Program

Development

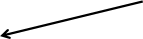
Optimized Inspection Program
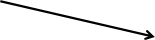
Risk Based Program
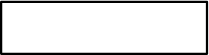
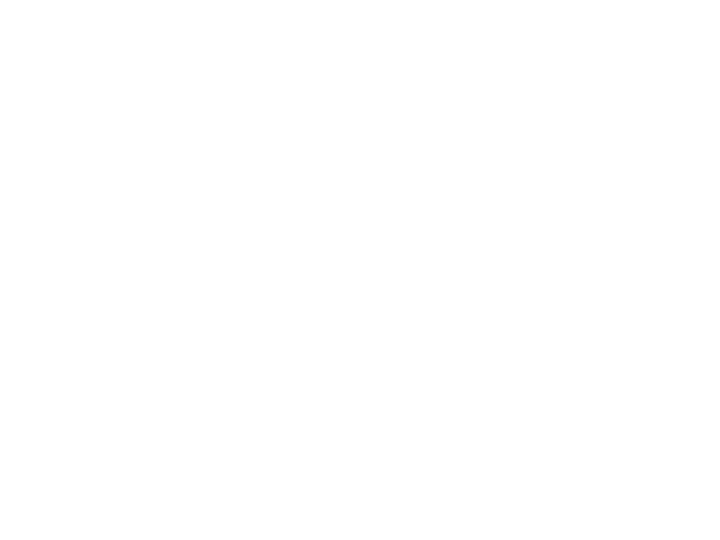
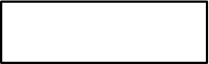
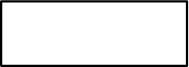
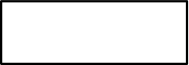



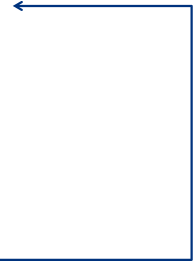
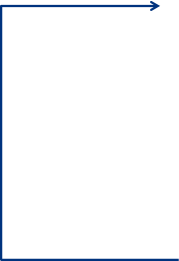

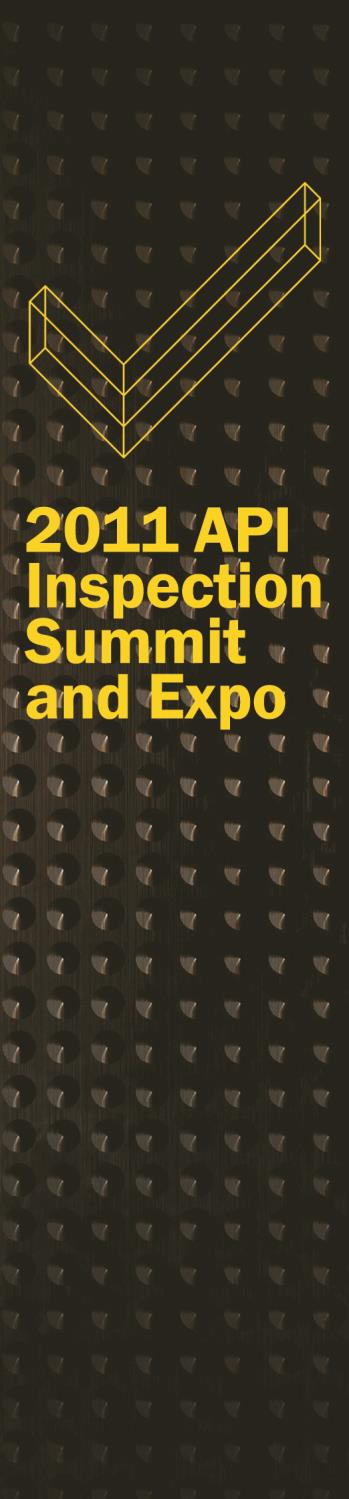
Inspection Plan Development
Critical to develop credible inspection plan
• Collect quality data, evaluate, validate and manage fixed
equipment data
• Historical inspection and maintenance records
• Damage assessment, damage rate and key operating variable
driving damage (integrity operating window, IOW)
• Develop specific inspection requirements based on operation
of plant and complexity of operation
Prioritize Equipment inspection
• Inspection due dates versus internal accessibility and expected
damage
Define criteria for inspection
• Acceptable damage for continued operation
• Fitness for service assessments, as required
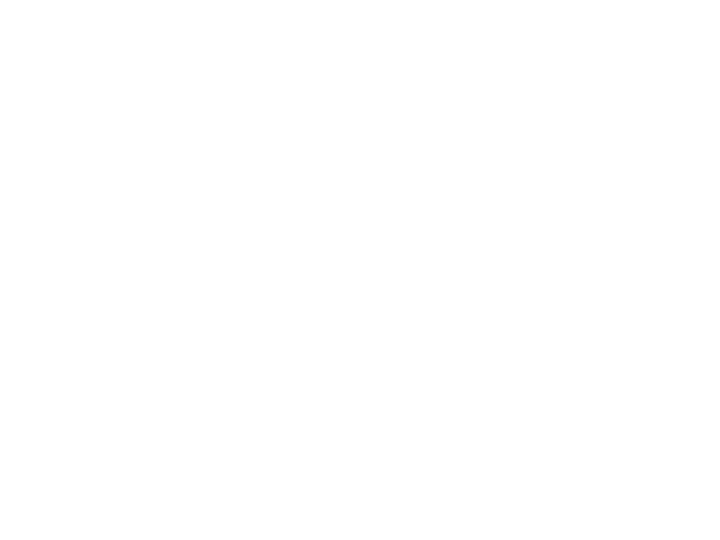
• Repair/Replacement criteria