Piping Circuitization and Risk-
Based Inspection Requirements
by Lynne Kaley, P.E.
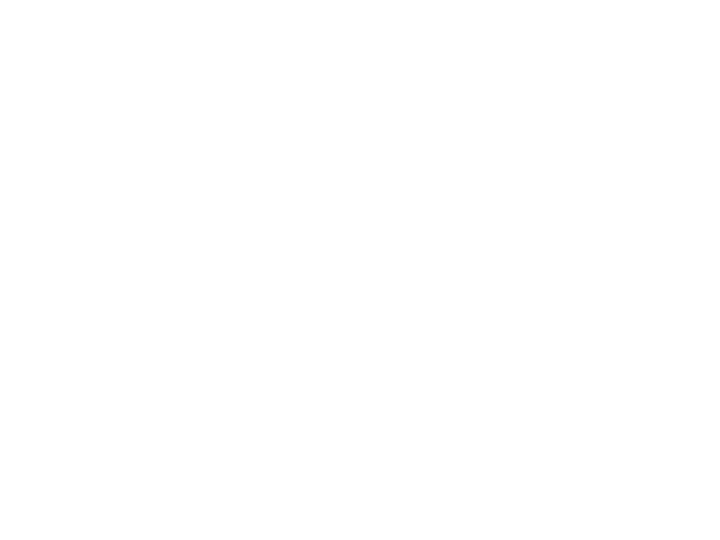




•
•
•
•
•
•
•
Materials/Corrosion and Risk Management
Engineer
30 Years Refining, Petrochemical and Midstream
Gas Processing Experience
Leader in Risk-Based technology development for
plant applications
Project Manager of API RBI Joint Industry Project
since 1996
Member of API committees for development of API
580 and API 581 recommended practices
Developer and Official Trainer for API 580/581
Public Training course
Vice President and Principal Engineer with Equity
Engineering
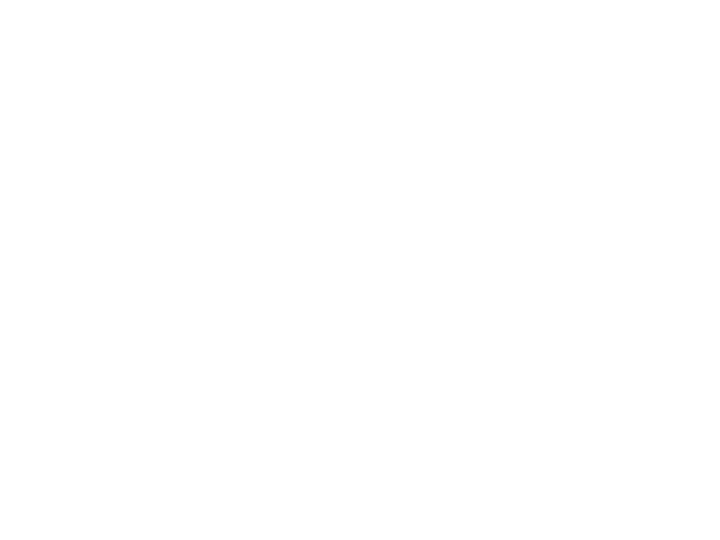




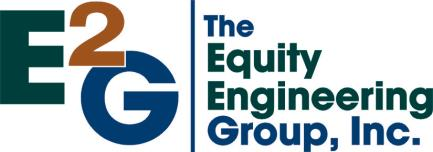


•
•
Purpose
Purpose of Presentation
– Using API 580 and 581 for piping Risk Assessment
– Systemization and circuitization of piping
– Understand complementary nature of Materials
Operating Envelopes (MOE)
– Understand challenges of piping inspection
Sources
– API RBI User Group Joint Industry Project
– API 580
– API 581
– API 570
– API 571
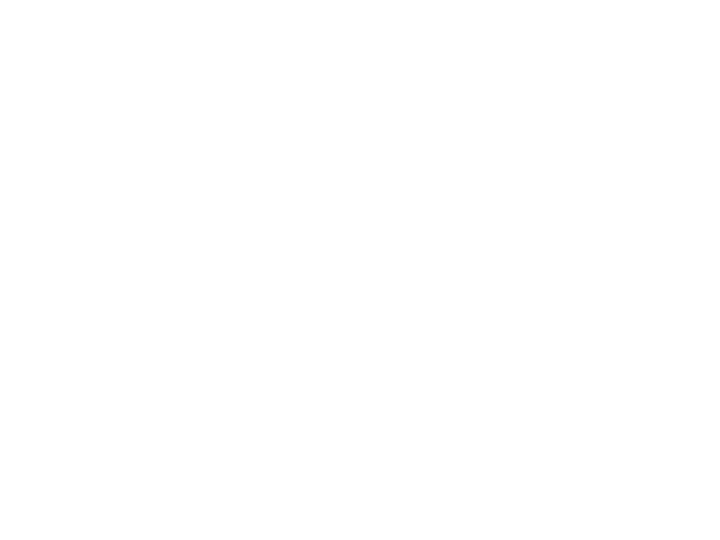



– API RBI Software
•
•
•
•
•
•
•
Presentation Outline
Introduction
Piping Programs Characteristics
Available Analysis Tools
A Complementary Approach: Material
Operating Envelopes (MOE)
Piping Systemization and Circuitization
– Piping study case study 1
– Piping study case study 2
Piping TML Data Analysis & Benefits
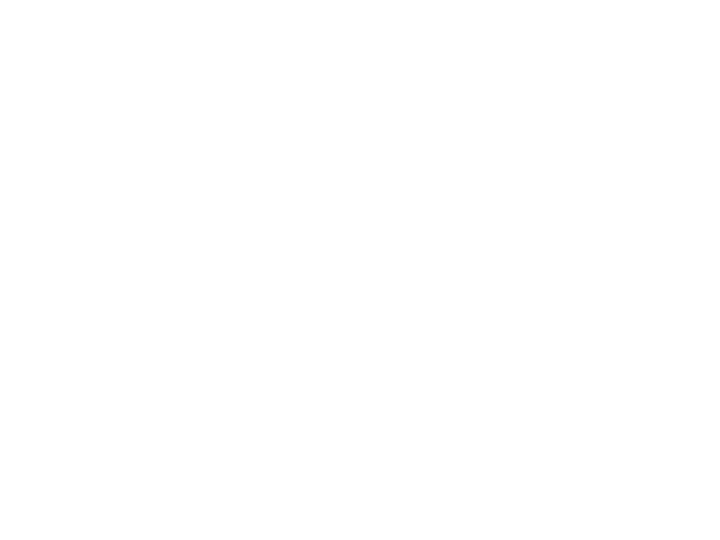



Summary & Conclusions
The Goal
Assure regulatory and corporate
compliance, and ensure reliable
use of piping (and equipment) for
finite run times, while measuring,
managing and minimizing risks
and eliminating non-value adding
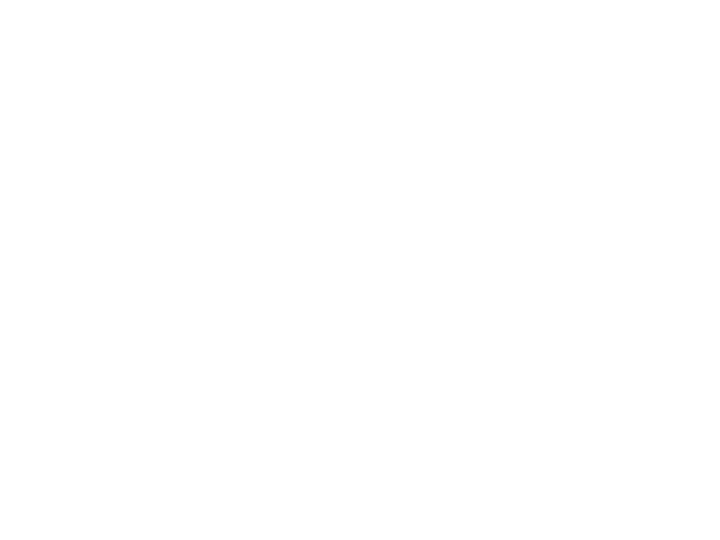



activities and costs.
The majority of industry piping programs use a classification
Quality of inspection data, coverage of inspection points and a
*Reference Marsh & McLennan, API Rand and E
•
•
•
•
•
•
Introduction
Historical industry statistics attribute piping failure to be
leading cause of large property losses
Industry data indicates that the most frequent unexpected
failures occur in piping systems (30-45%) due to localized
corrosion, often by undetected mechanisms
system from API 570 for criticality ranking
Straight beam ultrasonic inspection (UT) is the most
commonly used method for thinning damage detection
link of inspection locations and type to damage mechanism
must be analyzed to assure program effectiveness
Correct CML/TML placement needs to be determined in
conjunction with active damage mechanisms identified by
experienced corrosion/materials engineer
2G studies.
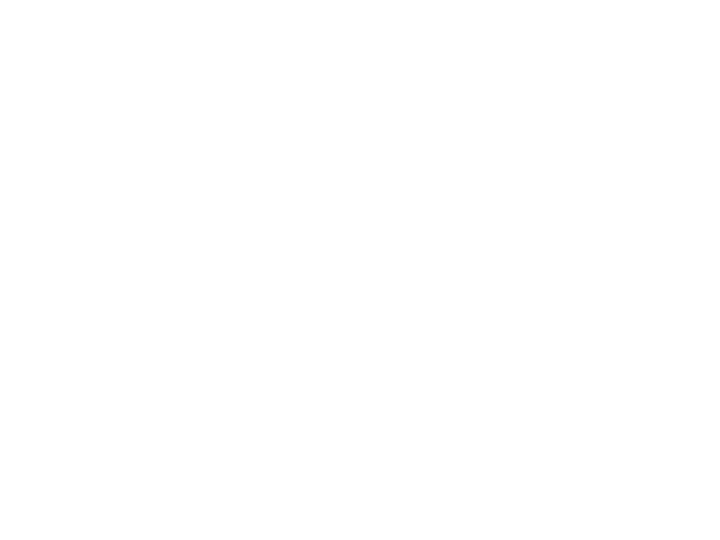



6
•
Introduction
“Losses in the refinery industry have
continued to increase over the last few years
and the causes highlight the aging facilities in
this category. A significant number of larger
losses (over $10,000,000) have been caused
by piping failures or piping leaks, leading to
fires and/or explosions. Several large losses
due to piping failures were due to corrosion
issues or using the wrong metallurgy…..”
From the Marsh and McLennan Report, The 100 Largest
Losses 1972-2001, 20th Edition: February 2003, a
publication of Marsh’s Risk Consulting Practice
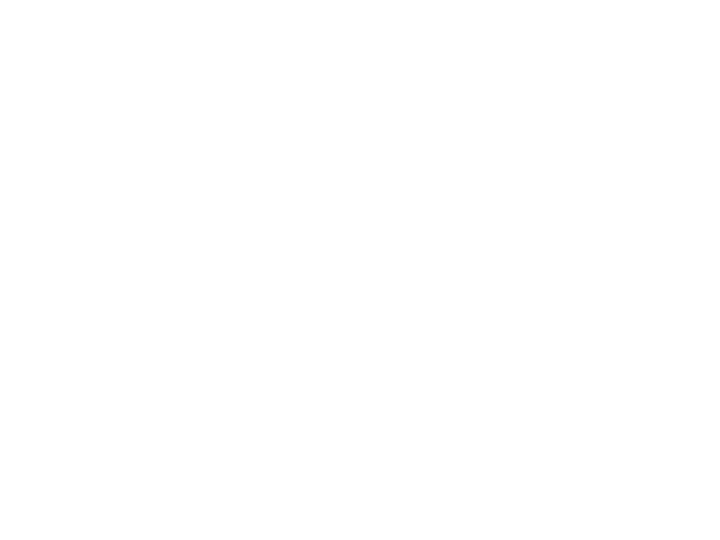



Introduction
The explosion occurred when employees were attempting to
isolate a leak on a condensate line between the NGL plant and
the refinery. Three crude units were damaged and two
reformers were destroyed. The fire was extinguished
approximately nine hours after the initial explosion. Five
people were killed and 50 others were injured. Initial
investigation into the loss indicates a lack of inspection and
maintenance of the condensate line.
June 25, 2000
Mina Al-Ahmadi, Kuwait
$412,000,000 (2000 dollars)
From the Marsh and McLennan Report, The 100 Largest Losses 1972-2001, 20th
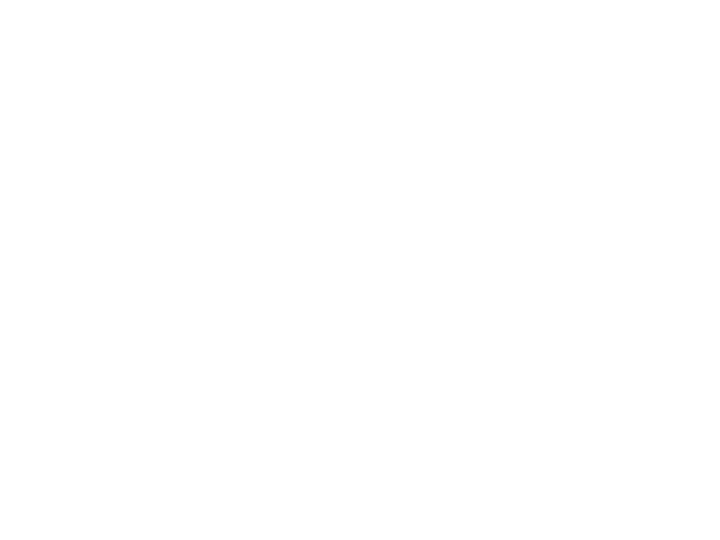



Edition: February 2003, a publication of Marsh’s Risk Consulting Practice
•
•
Introduction
Routine straight beam ultrasonic inspection (UT)
is by far the most common method (and often
the only) of inspection independent of the
expected damage mechanism assessment
Often a detailed analysis of the UT data is not
done to determine the quality of the data,
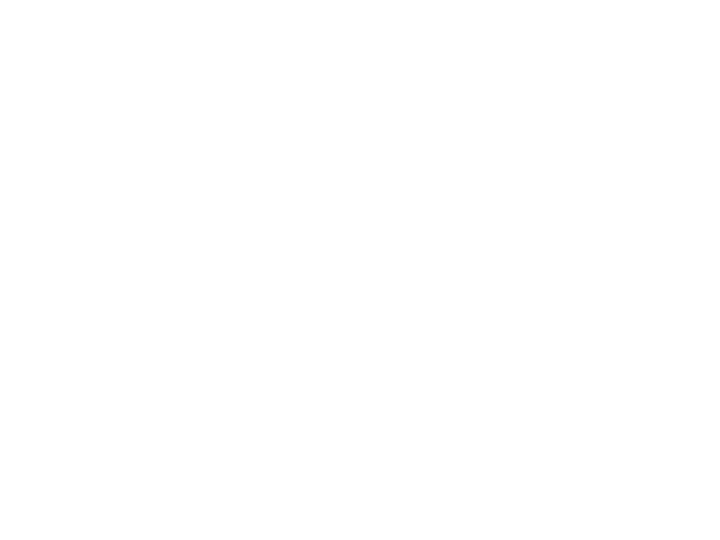



adequate coverage of inspection points, etc.
•
•
•
Introduction
Most refining, mid-stream, and chemicals
pressurized equipment was designed and built
for an operating basis different than current
operation
Plants continuously “tweak” the process to
raise throughput or process poorer quality
(lower cost) feedstocks (crudes or
intermediates)
Long term effect is cumulative so that minor
changes may cause a significant increase in
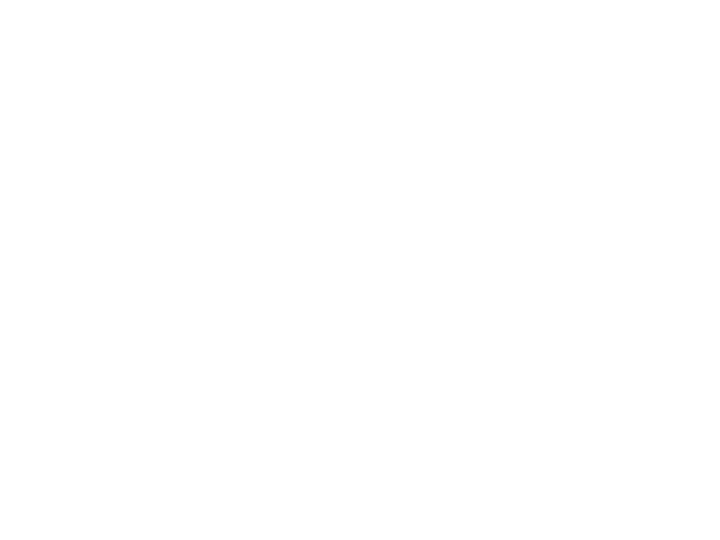



damage rates
•
•
•
Piping Programs
CMLs must be placed in the correct locations,
and used with appropriate NDE
– Guidance/Input from corrosion engineers for
placement decisions
– RBI not used to quantify risk reduction/investment
payback
– Use statistics as applicable to determine optimal
sampling
An overabundance of CMLs results in non-
value-added activities
Integrate and define the value of corrosion
reviews, Fitness for Service evaluations, RBI
and statistical analyses in the inspection and
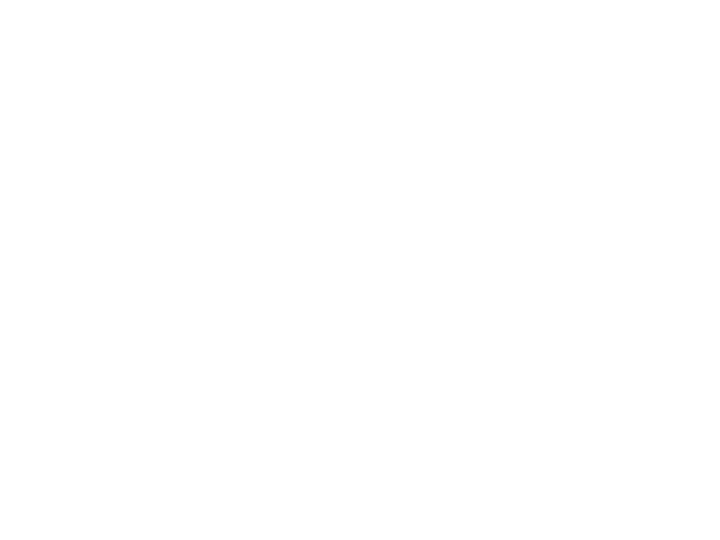



planning process for optimal effectiveness