Benefits of Risk Based Inspection
to the Oil & Gas Industry
Paper to be presented at the Oil & Gas Conference,
Perth, Australia 27-28 April 2000
Jens P. Tronskar
Lynne C. Kaley
Det Norske Veritas Pte Ltd, Det Norske Veritas,
Singapore Houston, Texas USA

ABSTRACT
A methodology for RISK BASED INSPECTION (RBI) has been developed by the American
Petroleum Institute’s (API) Committee on Refinery Equipment and Det Norske Veritas
(DNV). This methodology has been documented in the “Base Resource Document for Risk
Based Inspection” [1], which serves as the basis for the draft API recommended Practise RP
580 on application of RBI.
RBI combines knowledge of damage mechanisms and damage progression rates, inspection
effectiveness with load and resistance models to determine the probability of failure causing
leaks. It also combines the probability of failure with the consequence of failure to obtain the
risk. Conventional risk assessment methodologies are used to assess the consequences of
these leaks. A quantified ranking of process equipment and piping in terms of personnel and
environmental risk, loss of production and damage cost, focuses the inspection towards high
risk components and potential/active inspectable damage mechanisms for an optimal
utilisation of inspection resources on key assets. In any plant a relatively large percentage of
risk is usually associated with a small percentage of the equipment. A risk Based Inspection
approach permits the shift of inspection and maintenance resources to provide a higher level
of coverage on high-risk items and an appropriate effort on lower risk equipment.
In the refining and petrochemical industries, the use of risk analysis for inspection planning
and as a decision making tool for cost benefit analysis (CBA) of inspection and maintenance
activities is gaining industry acceptance. DNV has over the past three years conducted more
than 100 RBI analyses of refinery units, petrochemical and chemical plants. This extensive
experience shows that substantial cost savings can be achieved by optimisation of the
inspection without compromising on safety.
This paper briefly presents the RBI methodology and gives examples from the industry that
demonstrates the value of this novel technology.
Page 1 of 14
14
Benefits of Risk Based Inspection
to the Oil & Gas Industry
“Sweat your Assets Safely”

1.
INTRODUCTION
Recently the petrochemical and refinery sectors have
been facing tougher safety and environmental
regulations as well as challenges associated with need
for cost reduction to improve competitiveness and
ensure marginal returns in a situation of economic
slowdown.
Under these circumstances management of operational
risks, through utilizing of cost effective technology
and best practises for inspection and maintenance
planning is crucial.
RISK BASED INSPECTION (RBI) is the latest
technology for cost effective maintenance and
inspection. RBI prioritises these activities on the basis
of risk. RBI should be considered in a wider
perspective as a tool within the overall Risk
Management. Leaks of flammable/hazardous material
may originate from a variety of causes, and material
related damage which is considered by RBI, is only
one of these causes. Important other causes for leaks
can directly or indirectly be associated with process
upsets, failure of control systems, operator errors,
incorrect operation, improper job training, lack of
procedures for maintenance, bad weather conditions,
etc. Inspection cannot prevent leaks associated with
these causes however, statistics show that 40-50% of
losses due to leaks in the Hydro Carbon industry can
be attributed some form of mechanical failure, hence
inspection is an important activity to prevent failure.
2. METHODOLOGY
Analysing all equipment items in a plant can be a time
consuming effort; thus methods should be used to
minimise the work and to focus on the high risk items.
A screening of the plant systems in terms of risk is an
efficient tool for this – the screening involves a
qualitative RBI analysis. The systems ‘screened out’,
i.e. systems with low risk will be candidates for
corrective maintenance. The systems/items ‘screened
in’ will be analysed in more detail using a quantitative
technique. In this way time and effort are saved in the
data gathering process for low risk items. For detailed
inspection planning and in particular for cases where
one wishes to extend the inspection intervals beyond
code or statutory requirements, a detailed analysis
approach, should be applied in combination with a
more rigorous remaining life assessment i.e. refer to
API 579, than ordinary code (API 510/570 or 653)
calculations.
2.1 Qualitative Analysis
Page 2 of
DET NORSKE VERITAS
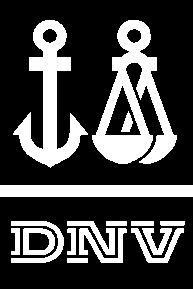

The screening process is done in close co-operation
with the operating company and should involve
experienced personnel from the plant (inspection,
operation and materials) in addition to personnel with
RBI assessment experience. This may be organised in
structured working sessions.
The first step of the analysis is to determine a factor
representing the probability of failure within the
selected area, then a factor for the consequences of
failure. The two categories of factors are subsequently
combined in the risk matrix to produce a risk rating for
the unit.
The risk matrix results, see Figure 1, can be used to
locate areas of potential concern and to decide which
portions of the process unit need the most inspection
attention or other measures of risk reduction. This
approach shows at a glance the number of equipment
items that are high or low risk, as well as whether the
risk is dominated by likelihood of failure (a good
candidate for inspection) or consequence of failure (a
good candidate for mitigation), or both. Likewise
components with low risk are identified and assigned a
corrective maintenance strategy.
The Qualitative method [1] also gives guidance on the
inspection interval for the various locations on the risk
matrix as shown in Figure 2. It is recommended that
detailed RBI should be performed for items where the
likelihood category is Medium High or High.
2.2 Quantitative Analysis
The quantitative RBI approach commences with the
extraction of process, equipment and other
information from the plant management database,
PFDs, P&IDs, material balance, inspection records.
Then each equipment item within the area of interest is
evaluated with regard to probability of failure,
consequence of failure and remaining life. The
consequence and probability for each scenario are
combined to obtain the risk. Both current and future
risk is estimated and based on the risk prioritisation the
inspection efforts are focused, aiming at opportunities
to reduce overall risk and cost.
2.2.1 Probability of Failure Analysis
The probability of failure analysis addresses the
material degradation that may take place in the various
components. This is done by considering the
environment/material interaction, actual design data,
operational history, experience with this or similar